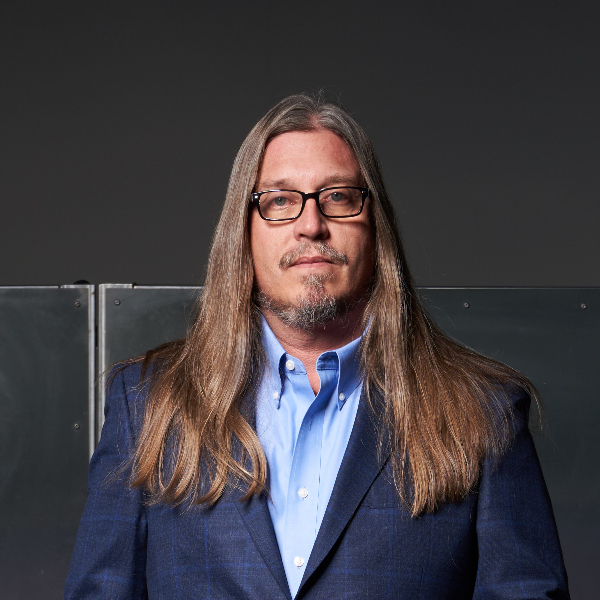
What is the state of innovation in the cannabis ancillary sector & how does it differ from mainstream, non-cannabis equipment manufacturing?
Cullen Raichart: It’s a hot sector. We have companies outside the cannabis industry adapting and re-purposing equipment from other manufacturing sectors in an attempt to take advantage of the fast-growing cannabis space. And, then there are companies who have been making cannabis equipment for some time, trying to grow as quickly as possible to keep up with demand and growing market opportunities.
Cannabis-specific equipment manufacturing is highly specialized. Cannabis is not like any other agricultural commodity. You can’t just take a mechanized system that processes cherries for example, and easily convert it to process cannabis.
The trichomes are too delicate. There is so much to consider with cannabis. Everything from preserving terpene content to the look of the final product has to be carefully considered.
You also have to respect that you are dealing with a final product that is medicine for many people, and it needs to be regarded with that in mind.
We are at the point where the race is on to invent never-before-seen solutions to the problem of processing large amounts of both cannabis and hemp quickly, while maintaining the high quality standards the market demands. Things are moving fast, and it’s a bit of a race to invent the best solutions.
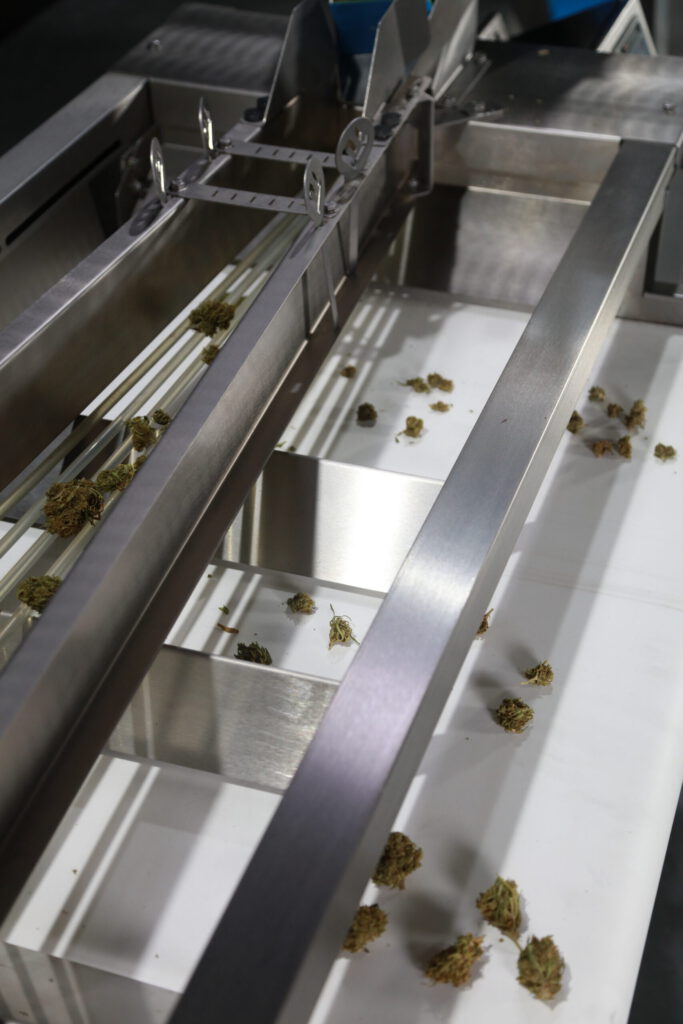
Are there specific advances in technology that you see contributing to innovation in the cannabis equipment manufacturing sector?
CR: The technology around manufacturing has gotten more sophisticated very quickly. The ways in which parts are manufactured has taken a giant leap in the last 3-5 years, due in large part to the intersection of advances in software packages and 3D printing technology.
We use 3D printers to make prototypes at GreenBroz, which allows our in-house engineering team to go directly from a whiteboard brainstorming session to printing out prototype parts faster than ever before. A process that used to take months now takes hours.
Our process begins with the 3D printer using SOLIDWORKS software, then we move to the Safan Darley press brake which uses Autopol Software, a modern 3D system for off-line press brake programming and unfolding of 3D CAD models. This system allows us to confirm with almost 100% certainty that we can manufacture a piece accurately and provides timing data for production steps, which is invaluable.
3D printing has changed everything for us, and allowed us to fine-tune new inventions in-house quickly. We don’t have to wait for a part to arrive from overseas, and we are not sending team members to China to oversee parts production. Design, prototyping, and production all happen under one roof at our Las Vegas facility.
We are moving in a direction where you will see 3D printing become central to not just R & D and prototype creation, but to manufacturing itself. You’ve got Elon Musk using the IDRA Giga Press die casting machine, pushing the envelope to make parts for his cybertruck.
Instead of just printing prototypes or molds, a molten alloy is placed in the press, and finished parts come out the other side. It’s essentially just like 3D printing. Czinger Vehicles is coming out with the world’s first printed hypercar, using its proprietary in-house invented Human-AI production system.
Large parts of the lightweight chassis are directly 3D printed, revolutionizing not just how cars are built, but significantly increasing efficiency on the production line.
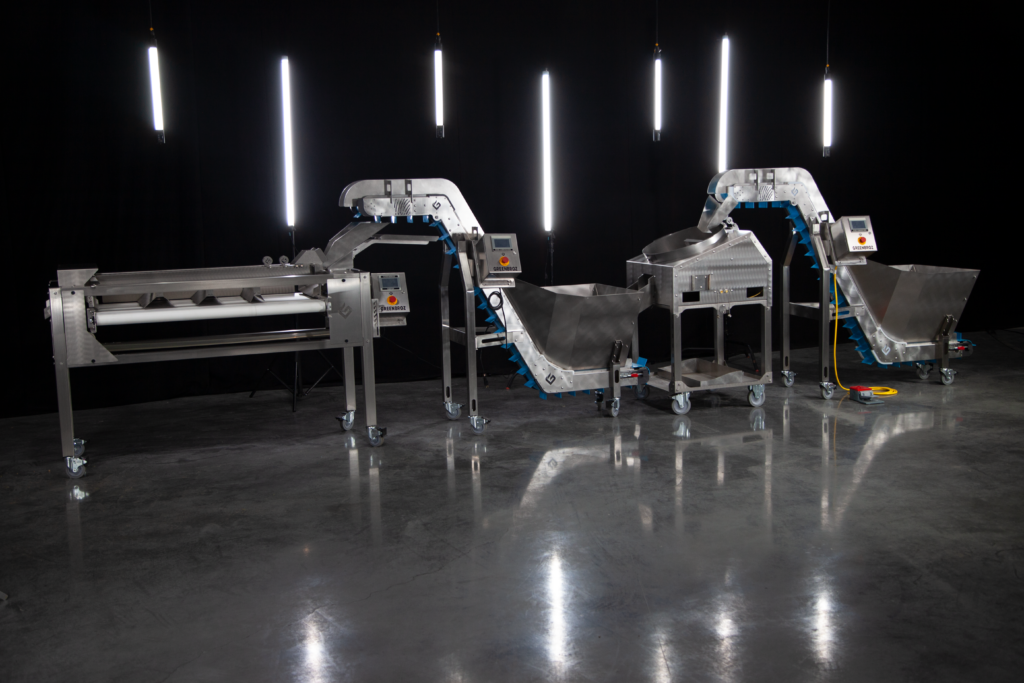
What are the unique challenges cannabis post-processing equipment ancillaries face?
CR: One of the biggest challenges we face is testing and proving that a new design works. Our team has a strong understanding of cannabis, but testing using such a high-value commodity can get a bit daunting.
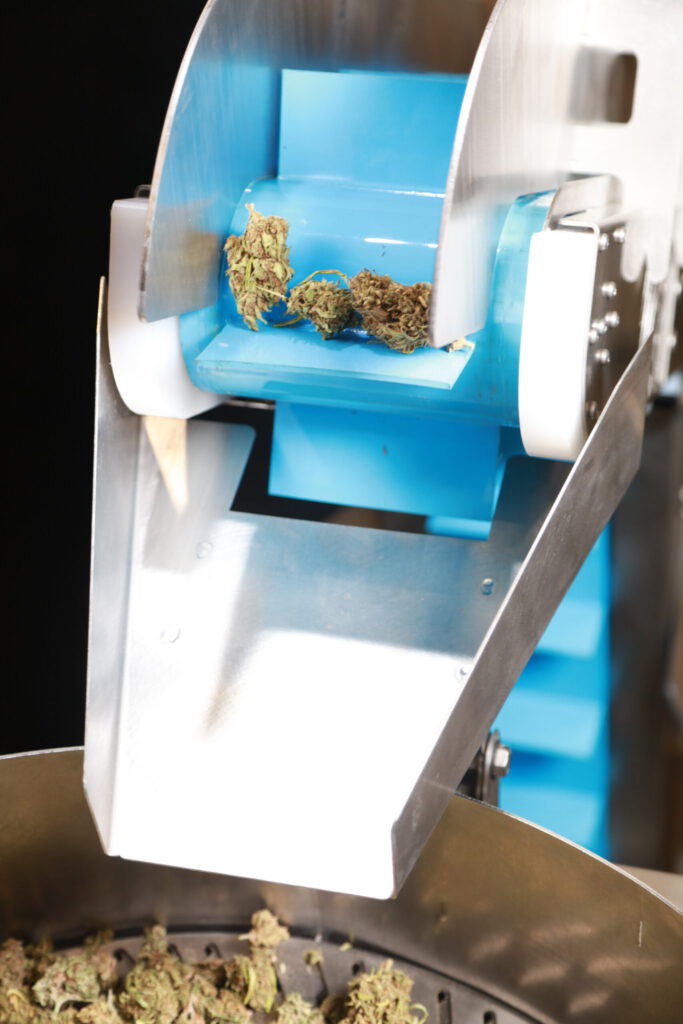
You really don’t want to destroy many thousands of dollars worth of product in the testing phase. We go a lot farther down the design road than a mainstream manufacturing company does before we go into product testing mode.
We use hemp to get close, but when you are confident that you have your design nailed down, you’ve got to test it with top shelf cannabis.
How has your company approached these challenges?
CR: We work with high-value producers, like The Clinic in Colorado. Through our partnership with them we are able to test our prototypes in real-world situations, and explore the boundaries of our designs.
Our team tests multiple strains under different environmental conditions to ensure that the equipment performs well across the board. We pride ourselves on being industry-born, and would never bring a machine to market that had not seen heaps of high-quality cannabis prior to launch. As painful as it is sometimes to do this type of testing on expensive raw material, there’s just no way around it.
What type of innovation is needed for the future for both cannabis and hemp processing?
CR: Customizable end-to-end post-harvest processing at scale is where we’re headed. The market is dictating the direction, and it’s clear that to gain the efficiency needed, automation has to be faster and smarter. Collecting information at each step in the automation chain is crucial, as is maintaining the high quality the modern market demands.
You’ll see less and less human touch which reduces the risk of contamination, as conveyors move product between processing stations. Everything will be automated from when raw material arrives at the processing facility all the way through to packaging and labeling. Increasingly companies need to make very careful data-driven decisions to remain competitive.
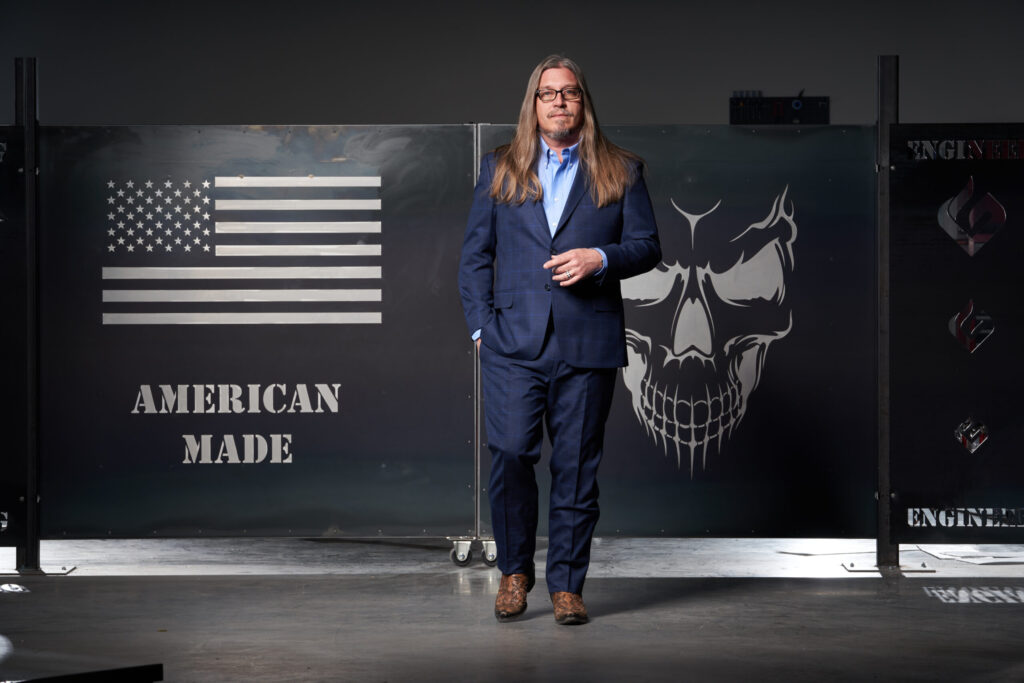
How will the (technology) landscape look different 5 years from now?
CR: We will see more homogeneous solutions across the sector. There will be more multi-state operators expanding their brand footprints across state lines, such as Cookies that have a need to standardize their SOPs. It’s like going into Starbucks.
Whether you’re in California or Nevada, that latte will be exactly the same. This kind of consistency can only be achieved when the processing is standardized at a high level.
Customized processing facility solutions that can be set up at scale and repeated accurately is the future.
There will always be a place for hand-trimmed or hand-finished craft flower from smaller producers, but this movement toward large-scale operations is an unstoppable tidal wave. If you want to grow and expand you have to ride the wave.
Sponsored Content