Pioneered by food safety companies, the cannabis industry is starting to use radio frequency disinfection processes to remove pathogens while maintaining quality.
How dirty is your pot? Odds are, it’s probably teeming with mold and mildew. In sizable markets such as Colorado and Nevada, as well as Canada, growers are required to report Total Yeast and Mold Count (TYMC) as part of their required regulatory compliance. If numbers exceed established minimums, whole crops and millions of dollars can be lost. Established technologies from the food industry are now being applied to the cannabis industry, allowing growers to overcome this risk and sell more product.
Yeast and mold are microbial pathogens. Depending on the type of grow, indoor or outdoor, they can be incredibly pervasive. It turns out, the conditions that are perfect for growing cannabis are also the ideal growing environments for mold and mildew.
Growers nationwide are looking for treatment options. Whatever option they choose should be affordable, scalable, non-toxic, and have little impact on the quality of the final product. There are a variety of methods available, though very few check all the boxes listed above. Traditional methods, like those examined below, compromise product integrity, and leave a lot of room for improvement.
Autoclave technology uses high heat, steam, and pressure differentials to sterilize products. Though this method is very effective at killing pathogens, it can also decarboxylate cannabis and produce a change in its color, taste, and smell.
Hydrogen peroxide is an affordable treatment for yeast and mold. It’s non-toxic, but only treats the surface of the plant and can cause oxidation throughout, removing terpenes and burning the cannabis.
Extraction is often the favored solution among growers facing a mold and mildew problem. It is one of the few methods of remediation approved by the Colorado Marijuana Enforcement Division. Supercritical gas extraction will kill nearly any contamination in one’s product; the drawback is the flower is now a concentrate, which is drastically less profitable.
Though each method has its appeal, there are few capable of treating the product without lowering its quality. That’s where technology from the food industry comes in. Food safety companies pioneered the use of radio frequency (RF), a proven disinfection process to reduce pathogens. This low-impact treatment is now being used in the cannabis industry and is ideal for killing contaminants while preserving potency and the product’s sensory qualities.
RF is non-toxic, organic, chemical-free, scalable, and effective. Total THC is preserved, moisture loss is minimal, and flavor and aroma are preserved.
RF machines excite the water molecules within the substance, creating friction and, consequently, heat. The machine closely regulates the temperature, heating the product to the exact point at which the mold is destroyed.
This method is highly effective and has been proven safe for the food industry for more than a decade. As such, it may become the preferred method for growers as the industry expands. We spoke with Arthur de Cordova, managing director at Ziel, a food and cannabis safety solutions company, to learn how radio frequency treatment technology is impacting the cannabis space.
Originally, Ziel worked closely with tree nuts – almonds, pecans, and macadamias. They developed their RF technology with University of California Davis to address a salmonella outbreak in almonds nearly a decade ago. It wasn’t until they were approached by the operations manager for a cannabis company in Pueblo, Colorado that the company decided to develop a machine specifically for the marijuana industry.
“There’s a very smart young man who we owe it all to. He found us online and went to an agricultural expo in California’s Central Valley, where we had a booth. We were showcasing our technology for the food industry and he showed up wearing a little backpack and tapped us on the shoulder.” De Cordova continued: “He said, ‘Hey, you guys are experts in remediating microbial pathogens such as salmonella and E. coli. Mold is a microbial pathogen too, so it’s under the same umbrella. Can you address this for our product?’ And that product was cannabis.”
De Cordova realized they would have to build a machine that would function specifically for this new product. “We moved from a very high-volume, conveyor belt system for our almonds, 2,500 pounds an hour, to a batch process of twenty pounds in less than 15 minutes.” They modified their existing technology to create a batch process that wouldn’t affect the integrity of the product.
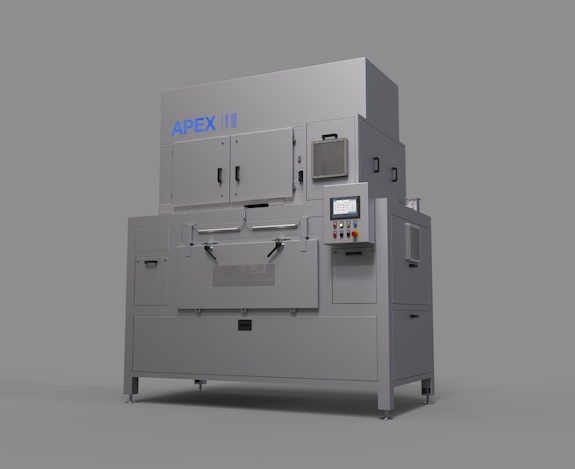
De Cordova went on to explain the process in more detail: “The RF system uses a set of probes to monitor temperature in real time. When we put a batch of twenty pounds of flower into the APEX, we insert six temperature probes in a range of flowers, because not all flower moisture is the same. If there is more moisture present, the dietetic – or volumetric – thermal process will occur faster. Once the flower hits a certain target temperature, the machine shuts off and the process is complete.”
This technology could be revelatory even in states without mold and yeast regulations. No one wants to breathe in pathogens, not to mention the poor flavor profile of mold. Mold- or yeast-laden products can harm a brand’s reputation. In an increasingly competitive market like marijuana, reputation is everything. Add to that the stringent regulations surrounding advertising and word-of-mouth recommendations become even more important.
RF has become the preferred remediation method for Los Suenos Farms, the largest outdoor cannabis farm in the country.
Los Suenos Farms Operations Manager Ketch DeGabrielle has been using Ziel’s APEX exclusively for the past three years. “After exhaustively testing and researching all treatment methods, we settled on radio frequency treatment as the best option. APEX allowed us to treat 100 pounds of cannabis in an hour – a critical factor when harvesting 36,000 plants during the October harvest.”
Author
-
Patricia Miller is an executive editor at Innovative Properties Worldwide. She explores science, technology, and policy shaping the legal cannabis sector. Follow her work when you subscribe to Cannabis & Tech Today at cannatechtoday.com/subscribe/ or visit her website https://patriciamiller.squarespace.com/.